1. Radiator design parameters input
The input parameters before designing the radiator include the heat that the engine needs to take away under certain operating conditions, the flow of coolant, and the location of the radiator.
2. Heat dissipation for car radiator
2.1 Heat dissipation Qw
The heat dissipation capacity of the car radiator needs to consider different vehicle working conditions, such as ambient temperature 40℃, sunshine intensity 1000w/m2, 40% humidity, high-speed climbing, Speeding on highway, etc.
Table1 Radiator assessment conditions
Engine radiator assessment conditions | Test conditions | |||
temperature(℃) | humidity(%) | Sunshine intensity(W/m2) | ||
1 | High-speed climbing | 40 | 40 | 1000 |
2 | Speeding on highway | 40 | 40 | 1000 |
3 | Low and medium speed variable speed climbing | 40 | 40 | 1000 |
4 | Rapid acceleration and rapid deceleration | 40 | 40 | 1000 |
5 | Other severe conditions | 40 | 40 | 1000 |
2.2 The radiator core area A, that is, the effective area of the radiator core
To calculate the core area A of the radiator, first calculate the required amount Va of cooling air for the entire cooling system. The volume flow Va of the cooling air is generally determined according to the heat dissipation Qw of the radiator.
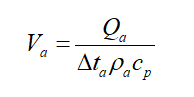
Calculate the core area of the radiator according to the cooling air volume flow Va:
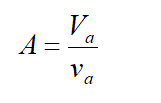
When the installation space allows, the larger core area is good for engine heat dissipation. However, the area of the core is generally limited by the size of the air intake grille and the mounting frame of the cooling module, and the area of the radiator core also affects the design of the condenser and the cooling fan.
2.3 The heat dissipation area S
The heat dissipation area S, that is, the sum of all the surface areas of the radiator cooling pipe and the radiator separator in contact with the air;
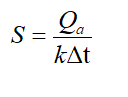
Qw-heat dissipation capacity of the radiator
Δt-Temperature difference between hot and cold liquid
K -The heat transfer coefficient, the unit is W/m2℃, represents the heat transferred per unit heat transfer area in unit time when the temperature difference between the hot and cold fluid is 1℃. Therefore, the K value represents the strength of the heat transfer process.
2.4 Core thickness D
D = S A×Φ
Note:
S -Cooling area(m²)
A -Core area(m²)
Φ-The compactness coefficient of the radiator core, the general range is: 500~1000m²/m³
2.5 Sectional area of radiator water tube and parameters of radiator fin
When the actual water flow velocity in the cooling water tube is 0.8~1.4m/s, the heat dissipation effect is the best. After 1.4m/s, it will not have much impact on the improvement of heat dissipation efficiency. As shown in Figure 1, the large size of the long axis a increases the thickness of the radiator, which increases the air pressure drop and increases the installation space of the radiator. b if it is too small, it will increase the liquid pressure drop and reduce the heat dissipation efficiency.
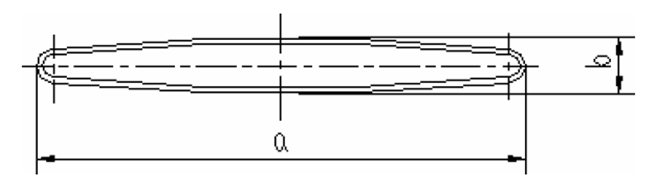
As shown in Figure 2: Fl is the height of the radiator separator, Fp is fin pitch, Ft is the thickness of the fin, L1 is the width of the fin, and Θ is the louvre angle of the fin. The size of the fin pitch Fp is very critical, it directly affects the density of the heat dissipation band. It is not good if Fp is too large or too small. If Fp is too small, it will increase the air pressure drop and reduce the heat dissipation efficiency. If Fp is too large, the cooling air cannot conduct sufficient heat exchange with the coolant in the heat dissipation water pipe, which will also reduce the heat dissipation efficiency. The fins are mainly to destroy the boundary layer of the cooling wind near the heat dissipation zone to improve the heat transfer efficiency.
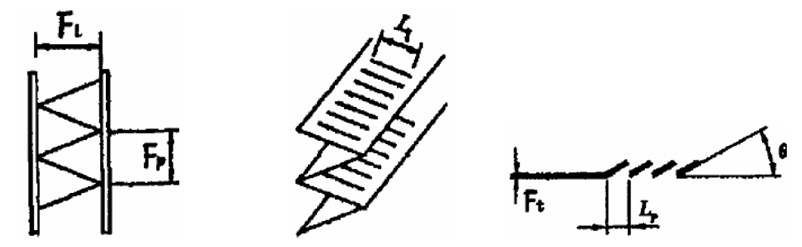
Heat transfer capacity and pressure drop usually increase proportionally.
Therefore, a key design question is: How to increase the heat transfer capacity without increasing the pressure drop, especially a certain size boundary?
At present, the selection and matching of various parameters of the radiator is mainly based on the establishment of the database. According to the needs, the similar radiator is selected for relevant performance and wind tunnel test verification, and then targeted improvements and optimizations are made to meet the requirements of use.
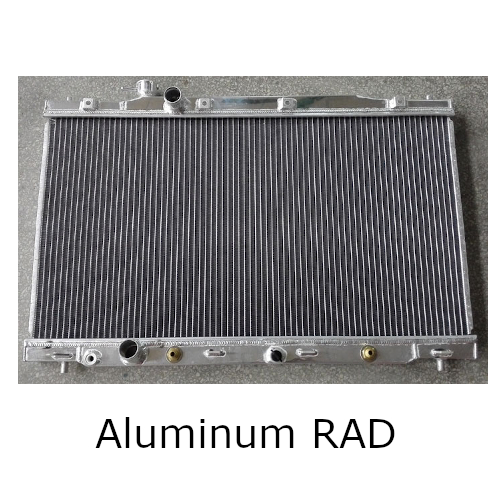
Know more about vehicle cooling system here.
Pingback: technical knowledge about how a car radiator expansion tank works – Fiter-Auto
Yes, it depends on the engine cooling module arrangement.