1.Aluminum alloy features
The density of aluminum is 2.7 g/cm³, which is about 1/3 of that of steel (7.8 g/cm³). Substituting aluminum alloy for steel can reduce weight by about 50%. Since the surface of aluminum is easily oxidized to form a dense and stable oxide film (passivation), it has good corrosion resistance. Aluminum has better castability, because aluminum has a low melting temperature and good fluidity, making it easy to manufacture parts with various complex shapes.So aluminum extrusion is possible. Aluminum is formed by adding one or several elements to aluminum, which can increase strength and hardness compared to pure aluminum. In addition to solid solution strengthening, some aluminum alloys can also be strengthened by heat treatment, so that the tensile strength exceeds 600 MPa. Aluminum alloys are widely used in radiator in car.
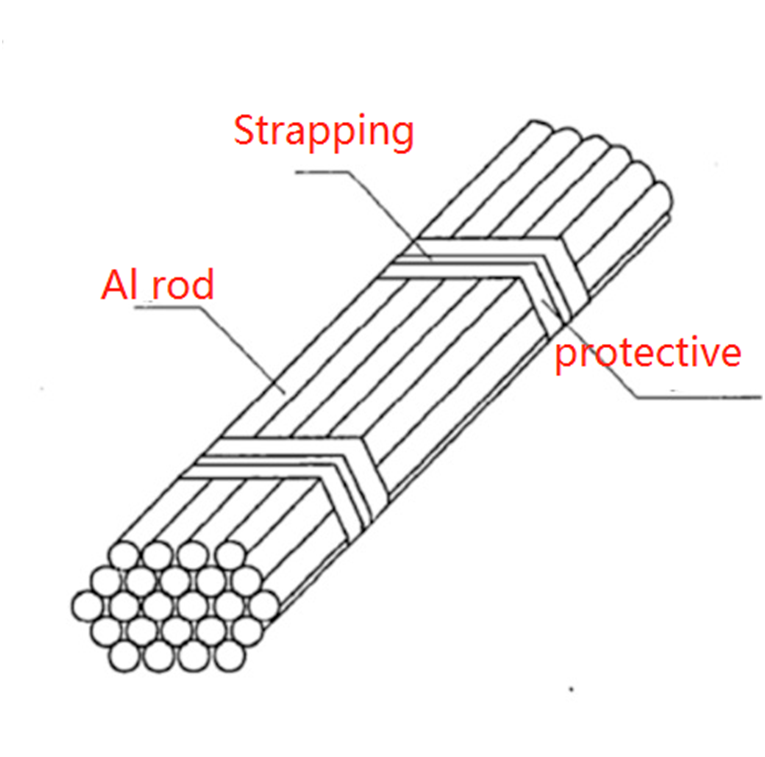
Table 1 Advantages of aluminum alloy
Nb.# | Main advantages | description |
1 | Low density | 1/3 of steel |
2 | Good corrosion resistance | Combined with Zn, it can form long-life aluminum that is not easy to corrode. |
3 | Flexible strength design | The strength at room temperature is not lower than that of cast iron |
4 | Beautiful surface | Colorless and transparent oxide film |
5 | Good machining performance | Low melting temperature, easy to cast into complex shapes; good cutting performance,aluminum alloy is widely used in CNC machining |
2.Pure aluminum and aluminum alloy series
Table 2 aluminum alloy series
Groups | series |
Pure aluminum (aluminum content is not less than 99.00%) | 1××× |
Aluminum alloy with copper as the main alloying element | 2××× |
Aluminum alloy with manganese as the main alloying element | 3××× |
Aluminum alloy with silicon as the main alloying element | 4××× |
Aluminum alloy with magnesium as the main alloying element | 5××× |
Aluminum alloy with magnesium and silicon as the main alloying elements and Mg2Si phase as the strengthening phase | 6××× |
Aluminum alloy with zinc as the main alloying element | 7××× |
Aluminum alloy with other alloying elements as the main alloying elements | 8××× |
Spare alloy group | 9××× |
3.Aluminum alloy base code
The basic principle of naming deformed aluminum and aluminum alloy state code: the basic state code is represented by an English capital letter; the subdivision state code is represented by the basic state code followed by one or more Arabic numerals.
Table 3 Basic code of aluminum alloy
Codename | name | Description and application |
F | Free processing state | It is suitable for products with special requirements for work hardening and heat treatment conditions during the molding process. The mechanical properties of the products in this state are not regulated. |
O | Annealed state | Suitable for processed products that have been fully annealed to obtain the lowest strength. |
H | Work hardened state | It is suitable for products whose strength is increased by work hardening. After work hardening, the product can undergo (or not) additional heat treatment (generally non-heat-treated reinforced materials) to reduce the strength. The state code behind the non-heat-treated strengthened aluminum alloy is generally the letter H plus three digits.For example,H112. |
T | Heat treatment state | (Different from F, O, H state) It is suitable for products that are stable after (or without) work hardening after heat treatment. The T code must be followed by one or more Arabic numerals (usually heat treatment strengthened materials).For example,T5. |
4.Aluminum and aluminum alloy heat treatment classification
4.1 Annealing
After the product is heated to a certain temperature and kept for a certain period of time, it is cooled to room temperature at a certain cooling rate. Through the diffusion and migration of atoms, the organization is made more uniform and stable, and the internal stress is eliminated, which can greatly improve the plasticity of the material, but the strength will be reduced. For a more precise answer, please refer to Wikipedia Annealing.
4.2 Solution quenching treatment
Heat the heat-treatable and strengthened aluminum alloy material to a higher temperature and keep it for a certain period of time, so that the second phase or other soluble components in the material are fully dissolved into the aluminum matrix to form a supersaturated solid solution, and then use a rapid cooling method Keep this supersaturated solid solution at room temperature, it is an unstable state, because it is in a high-energy state, solute atoms may precipitate out at any time. However, at this time, the plasticity of the material is relatively high, and cold working or straightening procedures can be carried out. For a more precise answer, please refer to Wikipedia solution quenching.
4.3 Aging treatment
After solution quenching, the material is kept at room temperature or higher temperature for a period of time, the unstable supersaturated solid solution will be decomposed, and the second phase particles will be precipitated (or precipitate) from the supersaturated solid solution and distributed around the aluminum grains. The strengthening effect is called precipitation strengthening. For a more precise answer, please refer to Wikipedia Aging treatment.
4.4 Retrogression and raging
After aging-strengthened, the aging alloy is heated at a certain temperature below the equilibrium phase or the solid solubility of the phase, the aging disappears will immediately disappear, and the original state will return to the fixed state. This kind of regression treatment occurs in this alloy. After the return, aging can be carried out again, and the regenerative hardening can still be carried out, but the aging speed will slow down, and the rest will not change much.For a more precise answer, please refer to Wikipedia retrogression and raging.
For different application requirements,such as forming,brazing quality and corrosion resistance,Aluminum alloys are selected by different temper state to balance these requirements.When the temper is defined,its production process is decided.